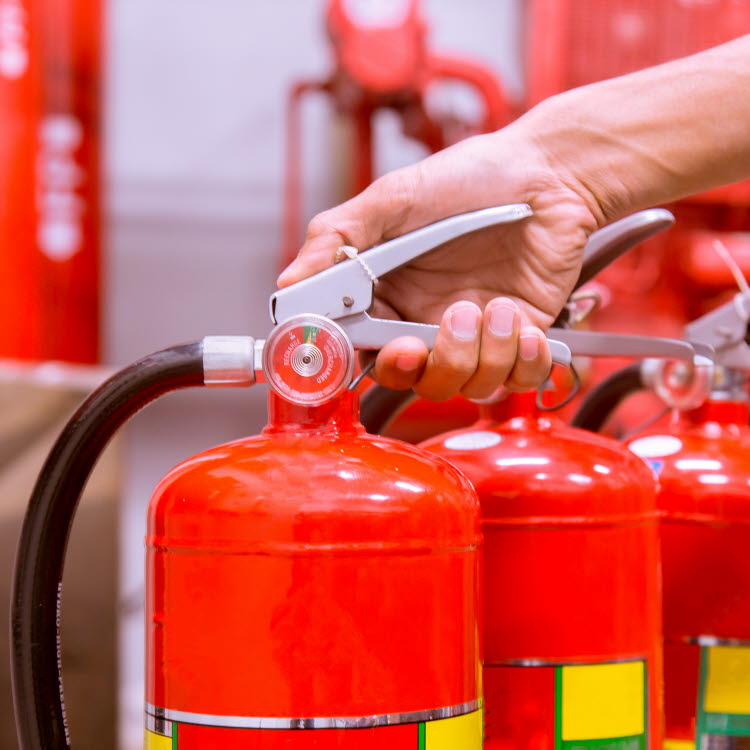
Fire Fighting
Fire fighting systems come in all shapes and sizes. AxFlow is able to provide a product or system for all of these be it a simple pump set to a complete integrated pumping system supplied by our partner Audoli & Bertola.
Fire fighting systems come in all shapes and sizes. AxFlow is able to provide a product or system for all of these be it a simple pump set to a complete integrated pumping system supplied by our partner Audoli & Bertola.