Progressive Cavity Fault Diagnosis
If you are experiencing issues with your Progressing Cavity Pump, the below guide can help you diagnose any issues.
Problem |
Possible Cause |
Remedy |
---|---|---|
Pump will not start |
Rotor & Stator Adhesion. |
Adhesion between Stator and Rotor due to prolonged period of inactivity. Lubricate rotor and stator with glycerin, or inert oil. |
|
Increase pump size or motor size. Change piping configuration/system set up to reduce pressure on the outlet |
|
Blockage |
Open inspection port to remove solids, if not possible to remove all, disassemble the pump and clean |
|
Fluid Temperature |
Clearances between rotor and stator are minute. If the fluid is outside the pump design range, the stator will suffer thermal expansion and burn against the rotor |
|
Solid Size |
The solid size is too large for the pump. Reduce pump speed or install a filter on the suction |
|
Sedimentation / Crystallization |
During inactivity, sedimentation or crystallization is occurring. Flush pump, disassemble and clean |
|
Frozen Fluid |
Temperature is too low with fluid freezing within the pump. Ensure the pump is protected from elements, drain when not in use or install trace heating. |
|
Stator Incompatible with fluid |
Check chemical compatibility |
|
Incorrect pump speed |
Check pump speed. Verify power absorbed, frequency, voltage and rpm. |
|
Viscosity too high |
Check against original pump specification |
|
Gland Packing |
Gland packing is worn too tight and requires loosening |
|
Inverter Settings / Wiring |
Check to start torque of the motor is correct as on initial startup power absorbed can be high meaning, if the torque is not set correctly on the inverter, it will not start the pump. Due to the friction between the stator and rotor it may be necessary to increase start-up torque. If an inverter is used an incorrect configuration of the parameters could cause problems. On motors with 7.5 kW or larger inverters, it is recommended to set an acceleration ramp of at least 4 s, whereas for motors with smaller inverters, at least 2 s.
This will reduce the stress at a start-up. Moreover, the starting rpm significantly affects the startup The torque is required to start the pump.
It is therefore recommended to reduce the pump’s starting rpm if any problems arise.
If forced air cooling is fitted to the motor and is not wired (requires wiring separately to the motor) then the pump may start and trip as it is not receiving sufficient cooling from the external cooling fan. |
|
Pump not creating suction |
Blockage |
Open inspection port to remove solids, if not possible to remove all, disassemble the pump and clean |
Fluid Temperature |
Clearances between rotor and stator are minute. If the fluid is outside the pump design range, the stator will suffer thermal expansion and burn against the rotor |
|
Solid Size |
The solid size is too large for the pump. Reduce pump speed or install a filter on the suction |
|
Sedimentation / Crystallization |
During inactivity sedimentation or crystallization is occurring. Flush pump, disassemble and clean |
|
Air Ingress |
Air Ingress through Seal or inlet pipework. Refit/replace the seal. Tighten bolts on joints. |
|
Frozen Fluid |
Temperature is too low with fluid freezing within the pump. Ensure the pump is protected from elements, drain when not in use or install trace heating. |
|
Suction Head too high |
Check inlet pressure, check inlet filter, check suction line is fully open. |
|
Low Pump Speed |
Pump speed too low for low viscosity fluids, and amounts to transfer too large. |
|
High Pump Speed |
Pump speed too high with viscous liquid. Risk of cavitation |
|
Direction of rotation |
Check the direction of rotation is inline with arrow on nameplate. Check drive coupling |
|
NPSH |
Check NPSHA meets NPSHR. Increase fluid level, lower viscosity, increase pipe suction diameter, reduce pump speed |
|
Dry Running |
Partially or fully running dry. Install dry protection probe |
|
Stator Worn |
Replace |
|
Rotor Worn |
Replace |
|
High Viscosity |
Check against pump specification |
|
Gland Packing |
Gland packing worn too tight and requires loosening |
|
Flow Rate Incorrect |
|
Increase pump size or motor size. Change piping configuration / system set up to reduce pressure on the outlet |
Blockage |
Open inspection port to remove solids, if not possible to remove all, disassemble pump and clean |
|
Air Ingress |
Air Ingress through Seal or inlet pipework. Refit/replace the seal. Tighten bolts on joints. |
|
Suction Head too high |
Check inlet pressure, check inlet filter, check suction line is fully open. |
|
Air Pockets |
Air pockets within the fluid. Check system. Slow pump, increase the level of fluid in tank, or deepen suction pipework. |
|
Low Pump Speed |
Pump speed too low for low viscosity fluids, and amounts to transfer too large. |
|
Dry Running |
Partially or fully running dry. Install dry protection probe |
|
Stator Worn |
Replace |
|
Rotor Worn |
Replace |
|
Transmission Broken or Faulty |
Check and repair where needed |
|
Incorrect pump speed |
Check pump speed. Verify power absorbed, frequency, voltage and rpm. |
|
High Viscosity |
Check against pump specification |
|
Gland Packing |
Gland packing is worn too tight and requires loosening |
|
Mechanical Seal |
Check seal faces for wear. Check seal compression. Replace worn items. |
|
Seal System |
Pump Seal System is unsuitable and requires changing. |
|
Uneven Flow |
|
Increase pump size or motor size. Change piping configuration / system set up to reduce pressure on outlet |
Air Ingress |
Air Ingress through Seal or inlet pipework. Refit/replace seal. Tighten bolts on joints. |
|
Suction Head too high |
Check inlet pressure, check inlet filter, check suction line is fully open. |
|
Air Pockets |
Air pockets within the fluid. Check system. Slow pump, increase the level of fluid in tank, or deepen suction pipework. |
|
High Pump Speed |
Pump speed too high with viscous liquid. Risk of cavitation |
|
Dry Running |
Partially or fully running dry. Install dry protection probe |
|
Stator Worn |
Replace |
|
Rotor Worn |
Replace |
|
High Viscosity |
Check against pump specification |
|
Excessive Pump Vibration |
Solid Size |
The solid size is too large for the pump. Reduce pump speed or install a filter on the suction |
Air Ingress |
Air Ingress through Seal or inlet pipework. Refit/replace the seal. Tighten bolts on joints. |
|
Suction Head too high |
Check inlet pressure, check inlet filter, check suction line is fully open. |
|
High Pump Speed |
Pump speed too high with viscous liquid. Risk of cavitation |
|
NPSH |
Check NPSHA meets NPSHR. Increase fluid level, lower viscosity, increase pipe suction diameter, reduce pump speed |
|
Drive Shaft |
Verify driveshaft movement. The transmission bush may be fitted incorrectly |
|
Stator Worn |
Replace |
|
Rotor Worn |
Replace |
|
Transmission Broken or Faulty |
Check and repair where needed |
|
Bearings Worn |
Replace Bearings |
|
Incorrect pump speed |
Check pump speed. Verify power absorbed, frequency, voltage and rpm. |
|
Pump seized or stopped pumping |
|
Increase pump size or motor size. Change piping configuration/system set up to reduce pressure on the outlet |
Solid Size |
The solid size is too large for the pump. Reduce pump speed or install filter on the suction |
|
Fluid Temperature |
Clearances between rotor and stator are minute. If the fluid is outside the pump design range, the stator will suffer thermal expansion and burn against the rotor |
|
Blockage |
Open inspection port to remove solids, if not possible to remove all, disassemble the pump and clean |
|
Sedimentation / Crystallization |
During inactivity sendimentation or crystallization is occurring. Flush pump, disassemble and clean |
|
Drive Shaft |
Verify driveshaft movement. The transmission bush may be fitted incorrectly |
|
Dry Running |
Partially or fully running dry. Install dry protection probe |
|
Stator Worn |
Replace |
|
Rotor Worn |
Replace |
|
Transmission Broken or Faulty |
Check and repair where needed |
|
Bearings Worn |
Replace Bearings |
|
High Viscosity |
Check against pump specification |
|
Stator Damage |
|
Increase pump size or motor size. Change piping configuration/system set up to reduce pressure on the outlet |
Blockage |
Open inspection port to remove solids, if not possible to remove all, disassemble the pump and clean |
|
Fluid Temperature |
Clearances between rotor and stator are minute. If the fluid is outside the pump design range, the stator will suffer thermal expansion and burn against the rotor |
|
Solid Size |
Solid size is too large for the pump. Reduce pump speed or install the filter on suction |
|
Sedimentation / Crystallization |
During inactivity sendimentation or crystallization is occurring. Flush pump, disassemble and clean |
|
Fluid Temperature |
Clearances between rotor and stator are minute. If fluid is outside pump design range, the stator will suffer thermal expansion and burn against the rotor |
|
Suction Head too high |
Check inlet pressure, check inlet filter, check suction line is fully open. |
|
High Pump Speed |
Pump speed too high with viscous liquid. Risk of cavitation |
|
NPSH |
Check NPSHA meets NPSHR. Increase fluid level, lower viscosity, increase pipe suction diameter, reduce pump speed |
|
Dry Running |
Partially or fully running dry. Install dry protection probe |
|
Stator Worn |
Replace |
|
Stator Incompatible with fluid |
Check chemical compatibility |
|
Incorrect pump speed |
Check pump speed. Verify power absorbed, frequency, voltage and rpm. |
|
Rotor Damage |
|
Increase pump size or motor size. Change piping configuration / system set up to reduce pressure on outlet |
Blockage |
Open inspection port to remove solids, if not possible to remove all, disassemble pump and clean |
|
Solid Size |
Solid size is too large for pump. Reduce pump speed or install filter on suction |
|
Sedimentation / Crystallization |
During inactivity sendimentation or crystallization is occurring. Flush pump, disassemble and clean |
|
Fluid Temperature |
Clearances between rotor and stator are minute. If the fluid is outside the pump design range, the stator will suffer thermal expansion and burn against the rotor |
|
High Pump Speed |
Pump speed too high with viscous liquid. Risk of cavitation |
|
NPSH |
Check NPSHA meets NPSHR. Increase fluid level, lower viscosity, increase pipe suction diameter, reduce pump speed |
|
Rotor Worn |
Replace |
|
Rotor Incompatible with fluid |
Check chemical compatibility |
|
Incorrect pump speed |
Check pump speed. Verify power absorbed, frequency, voltage and rpm. |
|
Seal Leakage |
Blockage |
Open inspection port to remove solids, if not possible to remove all, disassemble pump and clean |
Solid Size |
Solid size is too large for pump. Reduce pump speed or install filter on suction |
|
Fluid Temperature |
Clearances between rotor and stator are minute. If fluid is outside pump design range, stator will suffer thermal expansion and burn against the rotor |
|
High Pump Speed |
Pump speed too high with viscous liquid. Risk of cavitation |
|
Direction of rotation |
Check the direction of rotation is in line with arrow on nameplate. Check drive coupling |
|
High Viscosity |
Check against pump specification |
|
Gland Packing |
Gland packing is worn too tight and requires loosening |
|
Mechanical Seal |
Check seal faces for wear. Check seal compression. Replace worn items. |
|
Seal System |
The pump Seal System is unsuitable and requires changing. |
|
Drive Motor Generating Heat |
Adhesion between Stator and Rotor |
Adhesion between Stator and Rotor due to prolonged period of inactivity. Lubricate rotor and stator with glycerine, or inert oil. |
|
Increase pump size or motor size. Change piping configuration / system set up to reduce pressure on the outlet. |
|
Fluid Temperature |
Clearances between rotor and stator are minute. If fluid is outside pump design range, stator will suffer thermal expansion and burn against the rotor |
|
Incorrect pump speed |
Check pump speed. Verify power absorbed, frequency, voltage and rpm. |
|
Gland Packing |
Gland packing is worn too tight and requires loosening |
|
Insufficient Pressure |
Stator Worn |
Replace |
Rotor Worn |
Replace |
Positive Displacement Pump Repair
As the leading European supplier of positive displacement pumps we are experts in their repair
read more about positive displacement pump repair
Pump Servicing
AxFlow are one of the UK's leading pump repairs and offer local support across the country from our 5 regional bases.
read more about pump repair & maintenance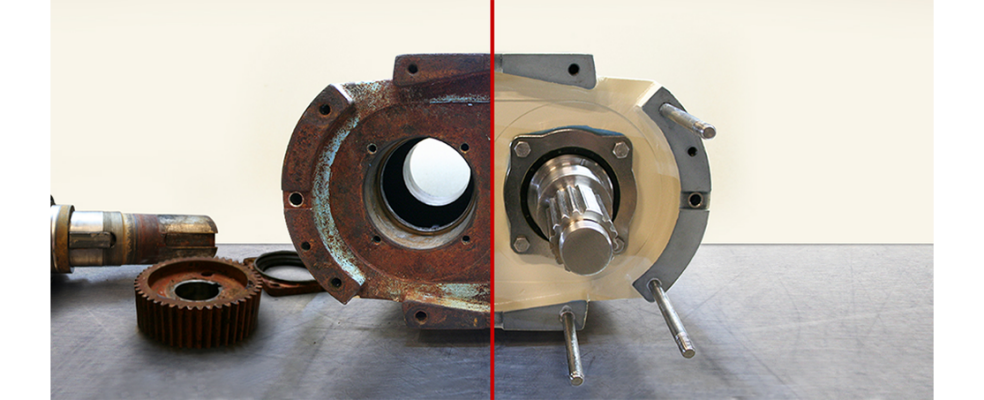